Low water pressure in the shower can turn an invigorating morning routine into a frustrating chore. When the flow diminishes to a mere trickle, it can be difficult to cleanse thoroughly, soothe aching muscles, or unwind under a steady stream of water. Recognising the nuances of why pressure falters is the first step towards restoring that satisfying cascade.
From household plumbing quirks to broader supply-side factors, multiple mechanisms might be at play. Understanding how each component—from your showerhead to municipal pressure regulators—interacts can help pinpoint the root cause. Armed with that knowledge, you can decide whether to tackle the issue yourself or bring in a professional.
.webp)
Common Causes of Low Shower Pressure
Before embarking on repairs or upgrades, it pays to identify which underlying issue is most likely responsible. Often, what seems like a complex problem can boil down to a blocked component or a simple valve adjustment. Other times, ageing infrastructure or water-supply regulations are to blame.
By inspecting the showerhead, evaluating pipe condition, and reviewing your home’s plumbing layout, you can narrow down the possibilities. A systematic approach prevents unnecessary expense and ensures that any fixes deliver lasting results. In the sections that follow, three key categories of causes are explored in detail.
Mineral and Sediment Buildup
Mineral-rich or sediment-laden water can leave deposits that restrict flow. Even small obstructions within the showerhead or pipes can significantly reduce output. Over time, these accumulations harden into a scale that demands more than a cursory rinse to remove.
- Hard water minerals such as calcium and magnesium precipitate when water is heated, forming a crust on internal surfaces. As microscopic particles embed in crevices, the effective diameter of flow channels narrows, causing the stream to weaken.
- Sediment from older pipes or poorly filtered municipal supplies can settle in elbows and valve seats, creating blockages that resist normal water flow. These particles may dislodge intermittently, resulting in inconsistent pressure.
- In areas without regular pipe flushing, iron and manganese compounds can oxidise within the system, leading to rust-coloured sediment that not only clogs but also corrodes metal components over time.
Clogged Showerhead and Flow Restrictors
Many modern showers incorporate flow-restricting devices to conserve water, but these can become clogged. Although intended to limit volume, they may degrade performance below an acceptable threshold when combined with debris. Cleaning or replacing these small parts often restores proper flow.
- Flow restrictor discs or aerator screens trap debris and scale while measuring out a capped volume of water per minute. Over long periods without maintenance, the fine mesh that regulates droplets can become nearly impermeable.
- Rubber gaskets and O-rings that seal around the restrictor can degrade, allowing sediment to bypass or accumulate in unintended areas. This degradation not only reduces pressure but may also cause leaks.
- If the restrictor mechanism is overtightened during installation or has become warped, it can pinch the waterway, compounding any sediment-related issues and leading to a barely perceptible trickle.
Pipe Age, Diameter, and Corrosion
Even clear showerheads cannot overcome undersized or corroded pipes upstream. As homes age, galvanised steel or older copper pipes corrode from the inside, reducing the cross-sectional area. Similarly, if the branch supplying the bathroom was installed with a smaller gauge than the main lines, the shower may always run underpowered.
Corrosion in steel pipes creates rough interior surfaces that increase friction and impede flow. Flaking rust fragments then travel downstream, risking further blockage in fixtures and valves.
Branch-line undersizing—such as using 15 mm tubing instead of 20 mm—can choke flow, especially if multiple outlets draw from the same run. Even a short section of smaller-diameter tubing can have a disproportionate impact.
In multifamily dwellings, shared risers and bends can become cumulative bottlenecks; tap usage elsewhere in the building can directly lower the pressure available at your shower, particularly during peak times.
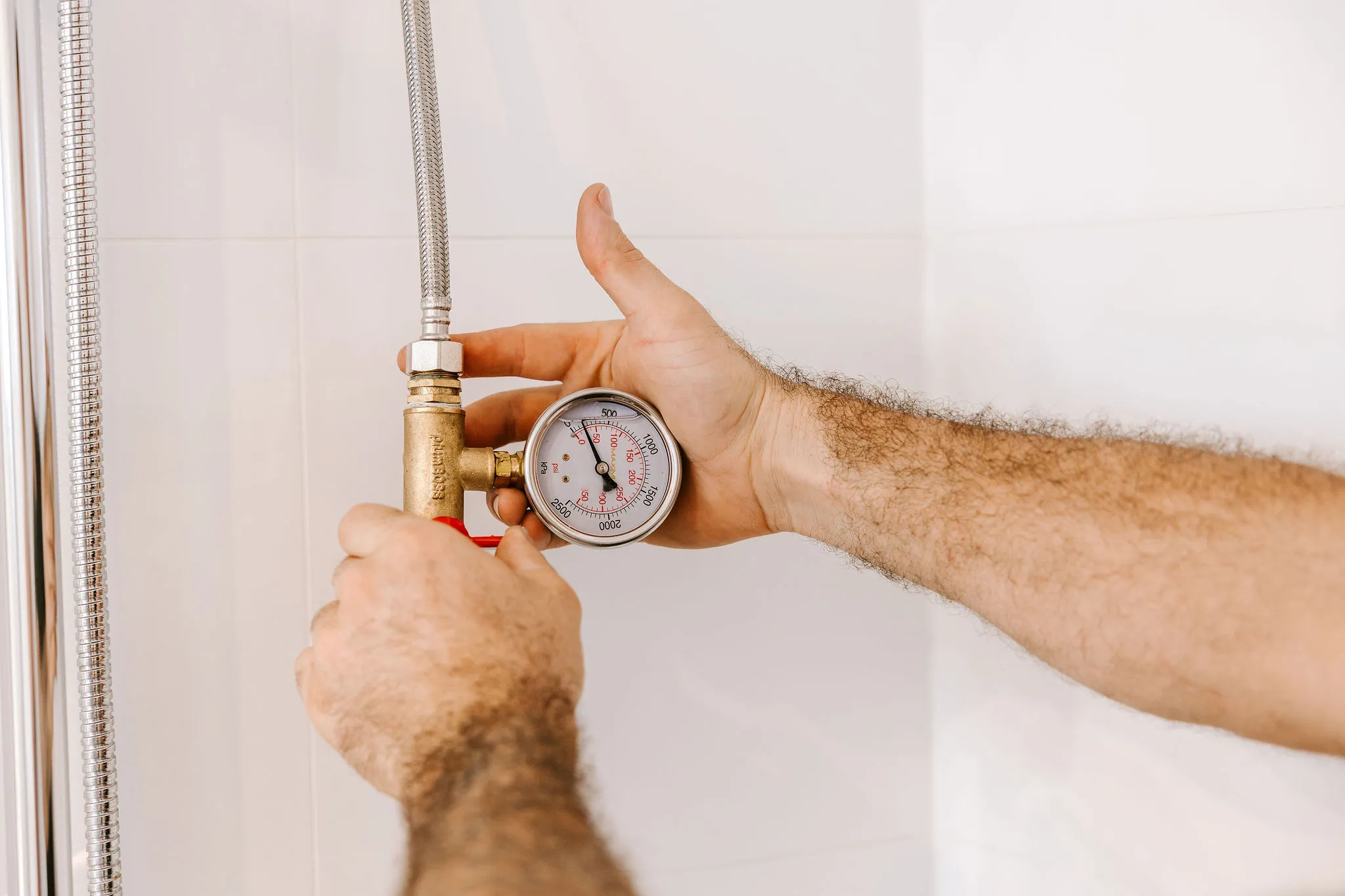
Is It a Plumbing Problem or a Water Pressure Regulation Issue?
Distinguishing between a defect in your internal plumbing and an external pressure regulation issue is crucial. The former often responds to targeted repairs, while the latter may require coordination with your water provider. Misdiagnosis can lead to unnecessary expense and frustration.
A plumbing problem generally manifests as isolated low pressure (affecting one bathroom or fixture), sound cues (gurgling or knocking), or visible leaks. Conversely, a pressure regulation issue tends to affect the entire property uniformly and may coincide with metre-or-main-line works in your neighbourhood. The subsections below illustrate how to tell the two apart.
Identifying Pressure Regulator Malfunctions
Pressure-reducing valves (PRVs) safeguard home plumbing from surges, but they can fail or drift out of calibration. Symptoms include sudden loss of pressure after an adjustment or a gradual pressure decline that cannot be explained by deposition or leaks.
- PRVs feature a diaphragm and spring mechanism that holds outlet pressure at a preset level. Mechanical wear, contamination, or spring fatigue can cause the valve to stick in a near-closed position, starving downstream fixtures.
- Symptoms of PRV failure often include banging noises (water hammer) as well as pressure surges when a fixture is activated. Inconsistent pressure across taps or strong flow in one outlet and a trickle in another strongly suggests regulator misbehaviour.
- External factors such as cold weather or sudden temperature swings can cause frost or condensation within the valve, leading to diaphragm stiffening. Over time, repeated freeze-thaw cycles can degrade the valve seals, necessitating replacement.
Assessing Plumbing Layout Deficiencies
Complex or poorly designed piping systems can introduce unnecessary resistance and pressure loss. Long runs, multiple sharp bends, and an overabundance of fixtures on a single branch all contribute to flow challenges. Reviewing your plumbing blueprint can expose these inefficiencies.
- Every right-angle turn in a pipe incurs pressure loss; clusters of bends in tight quarters—common in renovations—can reduce velocity and volume more than straight lengths of pipe.
- Cross-connections that bypass balancing loops or mixing valves can create back pressure that disproportionately affects certain outlets. Valves left partially closed during past repairs also contribute to reduced flow.
- In older properties, hidden junctions or abandoned branches may leave dead legs where water stagnates, causing temperature variation and sediment accumulation. These forgotten pipes can soak up pressure, reducing what reaches the showerhead.
Distinguishing Between Internal and Supply-Side Issues
A comprehensive test involves isolating internal and external elements. By turning off the PRV or main stopcock (if accessible) and briefly opening a garden hose or outdoor tap, you can compare garden versus shower pressure. If the garden spigot flows strongly while the shower remains weak, the culprit is almost certainly within your plumbing.
- If a standard garden hose drips when connected to the same supply line, the mains pressure at your property boundary may be low. Contacting the water utility to review local supply conditions is the next step.
- Conversely, if outdoor taps struggle as much as the shower, shared supply-side constraints such as hydrant-testing events or maintenance works could be the cause. Alerting neighbours for confirmation can expedite resolution.
- Seasonal variations—such as summer peak demand or winter pipeline flushing—can temporarily alter supply pressure. Keeping a log of performance at different times can reveal whether fluctuations align with external factors.
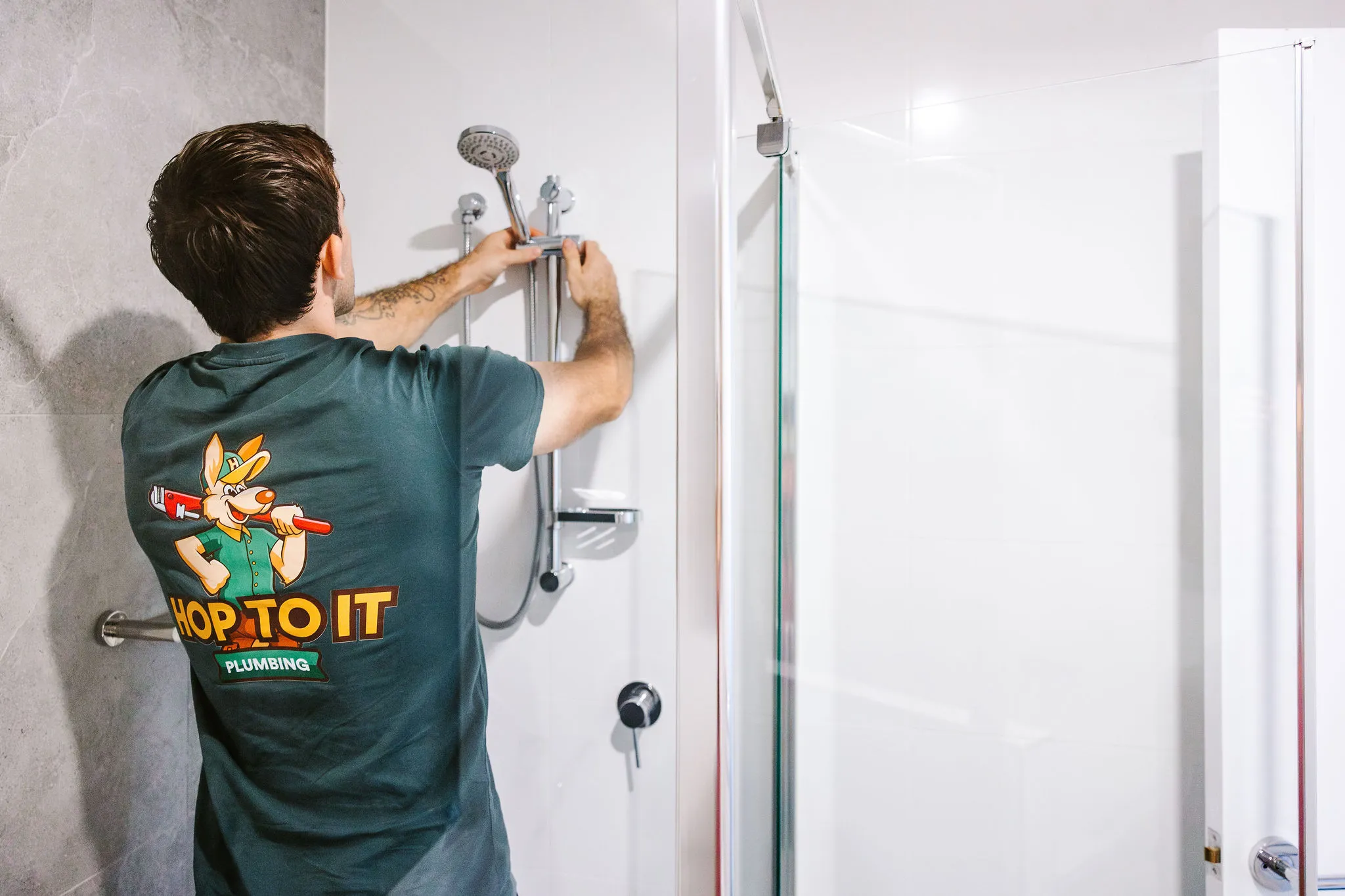
When to Call a Plumber for Diagnosis
While many minor obstructions can be cleared by a diligent homeowner, certain signs point towards professional intervention. Attempting complex repairs without sufficient expertise risks collateral damage, such as burst pipes or cross-threaded fittings. Recognising when to call in a tradesperson saves time and potentially expensive rectification work.
Seek expert assistance from a plumber in Brisbane when basic maintenance steps fail, when leaks or corrosion are detected, or when non-plumbing factors like electrical pump issues might be involved. A qualified tradesperson will have the specialised tools—pressure gauges, pipe locators, and flow metres—to diagnose ambiguous symptoms accurately. Below are key scenarios where a professional eye is warranted.
Persistent Low Pressure Despite Basic Fixes
If descaling, cleaning, or valve-tightening does not improve flow, it suggests a deeper fault. Professionals can conduct pressure-drop tests across sections of piping to isolate precise blockage points. Ignoring persistent issues may lead to complete fixture failure.
- A tradesperson can dismantle complex fixtures and flush individual sections of pipe, identifying stubborn scale that resists home-scale removers. They can also replace sections of flexible hose and internal valves that are rarely inspected.
- Technicians often carry specialised chemistry capable of dissolving built-up mineral scales in valves and restrictors without harming rubber seals or plastic fittings.
- If high flows return only temporarily—before pressure again diminishes—it suggests a dynamic blockage that requires a systematic pipe-by-pipe inspection, which is beyond the scope of routine DIY.
Signs of a Hidden Pipe Leak
Water loss due to undetected leaks can lower pressure while causing irreversible structural damage. Damp patches, mould growth, elevated water bills, or unusual hissing sounds in concealed spaces indicate a leak. Prompt professional repair is essential to prevent collapse or rot.
- Advanced leak-detection equipment, such as acoustic listening devices and infrared cameras, enables technicians to pinpoint underground or in-wall leaks without invasive wall or floor removal.
- A tradesperson can pressure-test isolated pipe segments, confirming line integrity and determining whether subterranean main-line or internal branch-line leaks are to blame.
- Early leak response not only restores pressure but also avoids extensive reconstruction work—saving both time and expense in the long run.
Unusual Operational Noises or System Fluctuations
Persistent banging, whistling, or rattling sounds often reflect water hammer, air entrapment, or failing valves. These symptoms signal that pressure fluctuations are occurring at the system level, which a professional can rectify. Ignoring these cues risks premature failure of fixtures and appliances.
- Water hammer arrestors can be installed or replaced to absorb shock waves generated by rapid valve closures, preventing sudden spikes that stress joints and pump seals.
- Air chambers may need bleeding or replacement if trapped air exacerbates pressure irregularities. Technicians know how to safely vent and rebalance closed-loop systems.
- A full diagnostic will reveal whether the root cause lies in pump controls, mixing valves, or shared riser configurations, guiding targeted interventions rather than trial-and-error fixes.
Fixes and Upgrades That Can Improve Shower Pressure
Once the problem has been diagnosed, a range of targeted remedies and enhancements can boost flow. From simple descaling solutions to repiping entire runs, the right approach depends on the severity of the issue. Strategic upgrades also future-proof your system against recurring pressure woes.
Whether you choose to undertake minor tasks yourself or engage a professional for major work, knowing available options helps you make informed decisions. The following subsections outline common fixes, regulatory adjustments, and more substantial pipe and valve replacements that deliver reliable pressure improvements.
Cleaning and Replacing Showerheads and Fixtures
Removing and soaking showerheads in a mildly acidic solution can break down the scale, while replacing old or inefficient models can yield immediate gains. Many manufacturers now offer low-maintenance designs specifically engineered to resist clogging.
- Soaking in a vinegar solution for several hours dissolves mineral deposits on stainless steel and brass components without damaging protective coatings. Rinsing and brushing afterwards restores nozzle function.
- Upgrading to models with larger nozzle apertures or wider spray patterns can improve the perception of volume even when actual flow remains unchanged, creating a more satisfying shower experience.
- Cartridge-based mixers can be swapped out with minimal disruption; modern cartridges often incorporate ceramic discs for smooth operation and reduced scale adhesion over time.
Adjusting or Installing a Pressure Regulator
If your home lacks a PRV or suffers from a maladjusted valve, installing or recalibrating one can stabilise pressure. A correctly set PRV ensures that upstream fluctuations do not compromise shower performance while also protecting downstream appliances.
- Professional plumbers will select a regulator sized to match your main incoming line, ensuring that supply pressure remains within the optimal range for both safety and performance.
- Adjustable models allow homeowners to fine-tune outlet pressure, balancing the desire for a strong flow with municipal water-use restrictions or manufacturer specifications on fixtures.
- Licenced installers will integrate any PRV modifications into an overall backflow prevention strategy, safeguarding potable water and complying with local plumbing codes.
Replacing or Upsizing Pipes and Valves
In cases where pipe corrosion or undersizing is to blame, repiping key sections with larger-diameter tubing or corrosion-resistant materials offers a long-term solution. Similarly, installing full-bore service valves can prevent internal constrictions that hamper the flow.
- Upgrading from 15 mm to 20 mm copper or cross-linked polythene (PEX) pipes in long branch runs reduces friction loss and supports higher peak demands without stress on joints.
- Stainless steel or PVC service valves replace corroded gate or globe valves that may not open fully, eliminating hidden pinch points that degrade over time.
- Comprehensive repiping projects often include rebalancing branch-line layouts and adding isolation valves, enabling targeted maintenance without shutting down the entire system.
A reliable shower experience comes down to understanding where the pressure loss is originating and choosing the right solution. Whether the culprit is a simple mineral deposit blocking the showerhead or a more complex issue like corroded piping or a malfunctioning pressure regulator, taking a methodical approach will save time and money. Basic maintenance—such as descaling fixtures and checking flow restrictors—can often restore strong flow instantly, but persistent or systemic problems warrant professional assessment. Engaging a qualified tradesperson ensures that hidden leaks, faulty valves, or undersized pipework are identified and rectified before they cause further damage. Ultimately, investing in the right combination of cleaning, adjustments, and targeted upgrades will deliver consistent, invigorating water pressure for years to come.